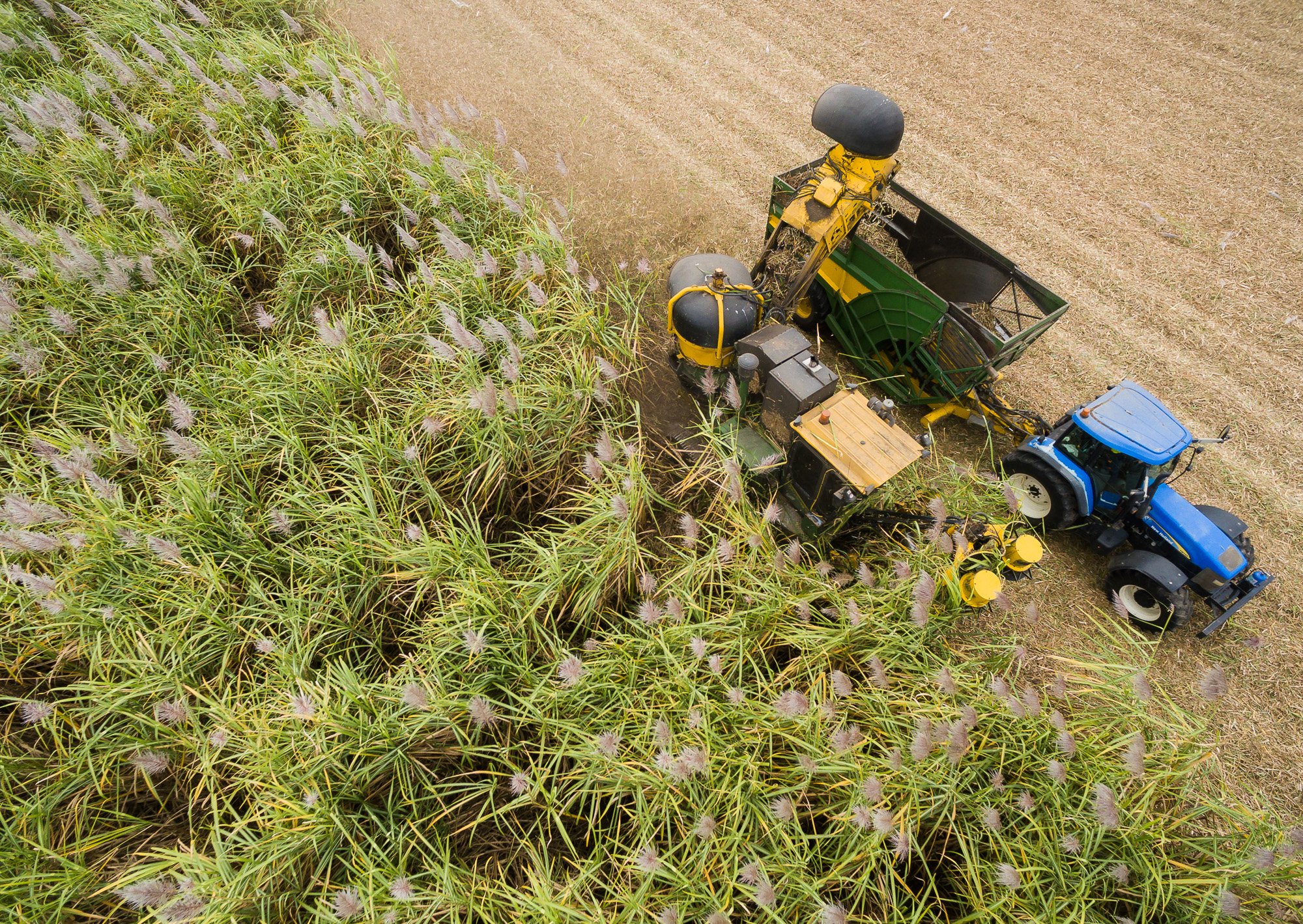
Expertise
What We Do
THE Sugar Cane Company
Experts in Sugar
Mackay Sugar is home to almost one third of Australia’s raw sugar exports and provides 45% of the raw sugar used by CSR for their refined sugar products stock on Australian supermarket shelves. We also produce other sugar-related products like molasses and mill mud that is used locally in Mackay by our growers.
On average, we produce about 700,000 tonnes of raw sugar each year - we are experts on sugar and on all aspects of sugar cane cultivation, and we know everything there is to know about raw sugar and its by-products: from production and management, right through to its characteristics and potential uses.
What We Do
Growing Sugar Cane
Sugar cane is a tropical grass – like bamboo – which grows to three to four metres tall and stores sugar (sucrose) during the growth period. The sugar forms naturally in the cane, needing water, carbon and the sun as an energy supply. To grow well, sugar cane needs warm sunny weather, free from frost, well-drained, fertile soil and water (around 1,500mm of rainfall per year or access to irrigation).
Mackay Sugar has key relationships with MAPS (Mackay Area Productivity Services) and SRA (Sugar Research Australia) who support our sugar cane producers through providing information and management advice around varieties, pest and disease issues, weed management, harvest management and agronomic practices. For example, cane varieties are developed by the SRA plant breeders and passed on to MAPS for propagation and distribution to growers.
Currently in the Mackay Region, there are more than 20 varieties of sugar cane being grown, each offering a unique set of attributes to suit a range of farming practices and environments. With adequate rain and sunshine, a sugar cane crop in our region typically takes between 12-18 months to mature. New cane is grown from buds that germinate on the stalks (billets), which are planted in the ground and typically sprout after two to four weeks.
The sugar is stored in the stalk and provides the cane with its energy requirements for its first leaves as part of its natural metabolism. When these leaves push through the soil, sunlight is available again as an energy source.
Once mature, crops are usually harvested between June to December. A mechanical harvester cuts the cane into 30cm lengths called billets, these are then collected and ideally transported to the mill within 16 hours.
Find Out More:
What We Do
Harvesting Sugar Cane
Sugar cane is harvested as the plant reaches maturity with the sugar that the plant has produced and stored in the stalk available in liquid form inside the cells as stored energy from the sun.
The harvesting process involves the use of specialised mechanical sugar cane harvesters with the bulk (> 95%) of the cane that is cut in our region being harvested via the “green cane trash blanket method”, which essentially means that the cane is harvested without prior burning. The cane is transported from the paddock to a Mackay Sugar rail or road siding where it begins the process of being transported to the mill.
What We Do
Sugar Production
The sugar “Crushing” season takes place each year, typically between June and December. This is the period where sugar cane is harvested in the paddock, supplied to our mills and “crushed” to make raw sugar and molasses.
Our Farleigh, Marian and Racecourse mills process sugar cane around the clock during the crushing season and greater than five million tonnes of sugar cane is converted into approximately 700,000 tonnes of raw sugar and 180,000 tonnes of molasses every year.
Once the cane arrives at the mill it is weighed and then shredded. The shredding breaks apart the fibrous stalks for access to the cells that contain the sweet juice.
Following this, the cane is crushed through a series of rollers, bursting the cells and separating the juice from the leftover fibrous material. The leftover material is used to fuel the mill's boilers. Having extracted the juice, impurities need to be removed. This is done by adding lime, heating and gravity settling of the solids formed. The clear juice is then concentrated by boiling under a vacuum into a syrup.
The syrup is further concentrated and seeded with small crystals and the crystals grow until they are large enough to be spun through a centrifuge to separate the crystals from the syrup. Once dried, these crystals are transferred to storage or transported to a refinery. The sugar at this stage is typically not food grade.
Find Out More:
What We Do
Sugar for the Food Industry
On average, Mackay Sugar produces approximately 700,000 tonnes of raw sugar each year. Raw sugar for the export market is delivered to the bulk sugar terminal at Port of Mackay.
Our raw sugar is exported predominantly to Asia, with refiners in South Korea, Indonesia, Japan and Malaysia as the primary customers. It’s also provided to the Sugar Australia Joint Venture for further processing and refining locally in Australia.
Our raw sugar is priced based on the Intercontinental Exchange No 11 Contract (a raw sugar futures contract) and we actively manage our price risk and exchange rate cover to enhance revenue.
What We Do
Farming Products
Molasses
We produce more than 180,000 tonnes of final molasses each year, of which 50,000 tonnes is sold to Graincorp Liquid feeds (near Marian Mill), where it’s processed as animal stockfeed. Approximately 50% of molasses produced is sold to the CSR Sarina distillery to be used in the production of ethanol, while the balance is exported via the Mackay Port, through Australian Molasses Trading.
Mill Mud & Ash
From the sugar manufacturing process, we produce mill mud and ash.
Mill mud (or filter mud) are remains after the cane juice is clarified and filtered. It contains soil from the sugarcane that enters our mills, sugar, bagasse particles and lime, which is used in the clarification process.
Ash is the material that remains after the combustion of fuel (largely bagasse) in our mill boilers.
These beneficial by-products are combined and distributed over farms as a soil conditioner and an important source of plant nutrients.
What We Do
Bagasse
Bagasse is a cane-fibre residue, and at Mackay Sugar we use bagasse as a renewable fuel, allowing our mills to be fully energy self-sufficient and enabling us to export green energy to the national electricity grid. We produce more than two million tonnes of bagasse each year, which is combusted in boilers to produce high pressure steam that drives the power houses and mill turbines. The exhaust steam is used to process the sugar juice.
Throughout the sugar crushing season (June to December) excess bagasse from Mackay Sugar mills is stockpiled and used as a biofuel in our factory boilers and in our Cogeneration Plant located at the Racecourse Mill site during the non-crush season. To ensure the safe and efficient transport of bagasse from our stockpiles to our factory boilers, we subcontract highly-specialised bagasse haulage services that ensure an all year-round supply of this important sugar production by-product.
As global demand for clean energy sources grows, several innovative companies are investigating several possible alternative uses for bagasse and Mackay Sugar proudly support many of these initiatives. At our Racecourse Mill site, the Queensland University of Technology (QUT) has established a Renewable Biocommodities Pilot Plant that is researching the production of renewable diesel and sustainable aviation fuel using bagasse.
What We Do
Green Electricity
Our Cogeneration Plant, which is situated at Racecourse Mill, uses sugar cane waste to produce enough steam and electricity for powering the mill and the co-located raw sugar refinery, as well as approximately one third of the Mackay region’s annual electrical power requirements; the equivalent of around 20,000 households (exporting approximately 115,000MWh).
Mackay Sugar’s Cogeneration Plant comprises a 150t/hr steam boiler, a 38 MW steam turbine as well as ancillary units such as a cooling tower, water purification, waste ash handling units, and supports several local jobs.
The waste product used to fuel the Cogeneration Plant’s steam boiler is known as bagasse, which is the leftover fibre from the sugar milling process. Bagasse is biologically derived in cane paddocks and all carbon dioxide emissions produced by the combustion process are circularly absorbed from the atmosphere by the growth of new season crops.
Throughout the sugar crushing season (June to Dec) approximately 220,000 tons of excess bagasse from Mackay Sugar mills are stockpiled and used to fuel the Cogeneration Plant during the non-crush season. By using bagasse and through careful planning and management, the electricity produced by Mackay Sugar’s Cogeneration Plant is almost carbon neutral and has proven to be a highly effective form of biomass green energy for the region.
Find Out More:
Download the ‘Sugar mills are a source of renewable power’ Fact Sheet
What We Do
Cane Transport
Mackay Sugar operates an extensive and highly specialised cane rail network, spanning 832 km across the Mackay region. From Wagoora in the north to Munbura in the south and west through the Pioneer Valley to Finch Hatton, our rail network ensures efficient transportation of sugar cane.
Upon harvesting, sugar cane is loaded into cane bins that boast carrying capacities of 5t, 6t, and 15t respectively. With a fleet of approximately 6,600 cane bins, Mackay Sugar ensures seamless logistics to accommodate varying yields from farmers. Train drivers gauge the tonnage behind them solely by weight, allowing them to adjust their driving accordingly.
These cane bins are towed to our mills by our fleet of 34 cane rail locomotives (locos). Our largest locomotive can transport up to 262 loaded cane bins, reaching a maximum speed of 38 kph. Each loco in our fleet is named after former sugar mills in the region, creating unique identifiers for communication and recognition. Ranging between 18 tonnes and 40 tonnes, our varied fleet ensures optimal movement of sugar cane, with different locos assigned to specific tasks.